100% Real-Time Induction Seal Inspection and Analysis
Induction sealed packaging is widely used in industries like food and beverage, pharmaceuticals, and cosmetics to provide product integrity, extend shelf life, and offer consumers a visual indication of whether the product has been tampered with. Typically, induction seal integrity is checked via sampling of the product itself, which often results in production inefficiencies and slowdowns.
Now, with Yoran’s revolutionary thermal imaging inspection solution, companies across the globe can realize a quantum leap in the inspection of induction seals with a range of features and benefits:
- Non-intrusive, non-degrading inspection of every induction seal (right through the cap)
- Operates at full production speeds with no slowdowns
- Process control to indicate not only if an issue occurs, but pinpointing what caused it
- Statistical data provided in real-time, allowing for immediate induction seal corrections and process adjustments without undue delays
- Tamper evidence integrity inspection
- Detection of caps that are not fully closed to avoid dangerous issues with child resistant closures
- Streamlined graphic unit interface (GUI) is simple to use and minimizes human error
- Reduces potential consumer complaints and protects brand reputation
- Immediate ROI by reducing costs associated with existing sampling methods
- Minimizes waste, product recalls, materials and labor
How does it work?
Yoran Imaging’s unique solution combines high-end thermal imaging typically used in the defense industry with sophisticated analysis algorithms and proprietary IP. This powerful combination provides real-time integrity monitoring of every single bottle or jar on the packaging line…without slowing down machine throughput.
The system automatically reads and analyzes the inherent heat signature of the cap’s liner (which is amplified directly after induction), providing immediate quality control data to the operator. The system is compatible with most bottle and cap sizes/types and can be seamlessly integrated into almost any packaging line.
Induction seal inspection and analysis detects through the closed cap.
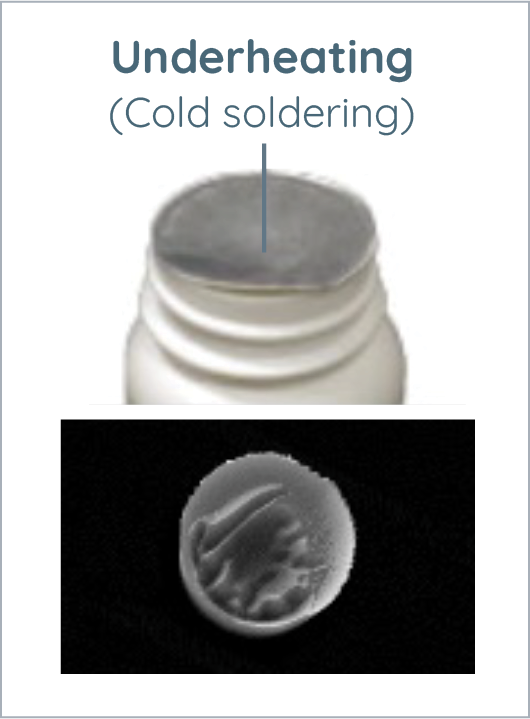
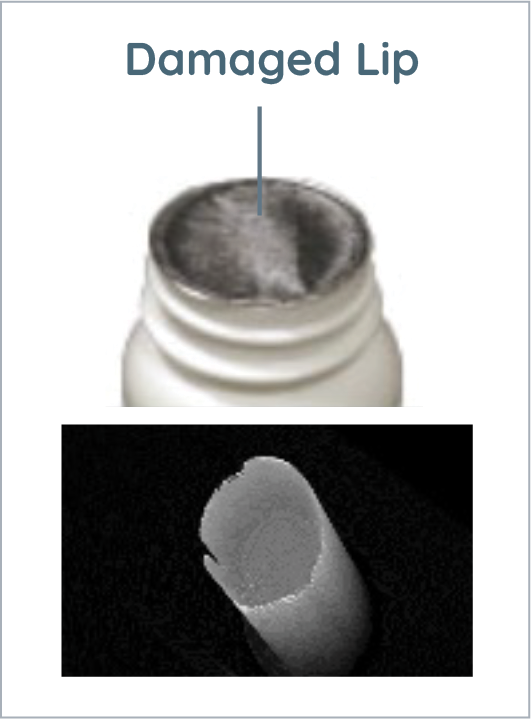
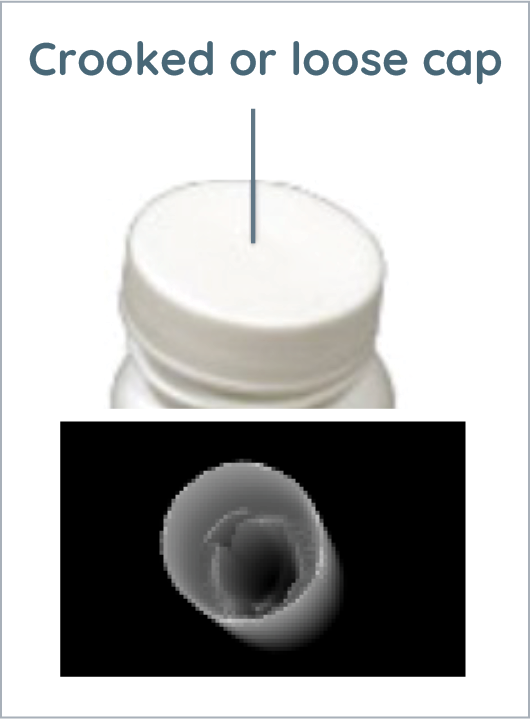
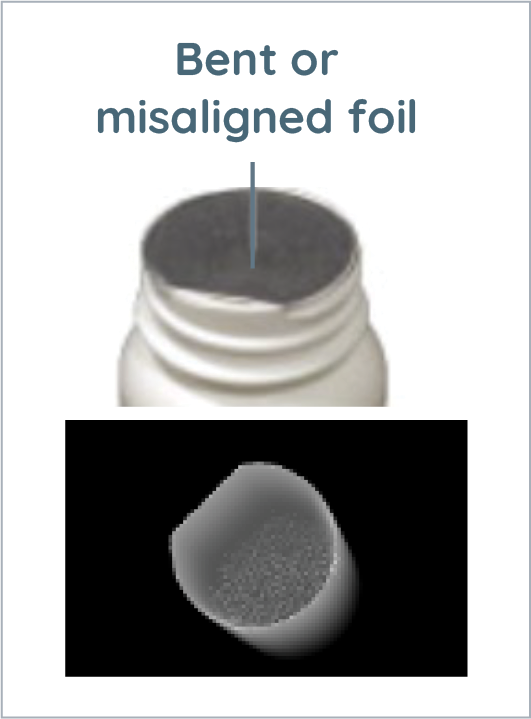
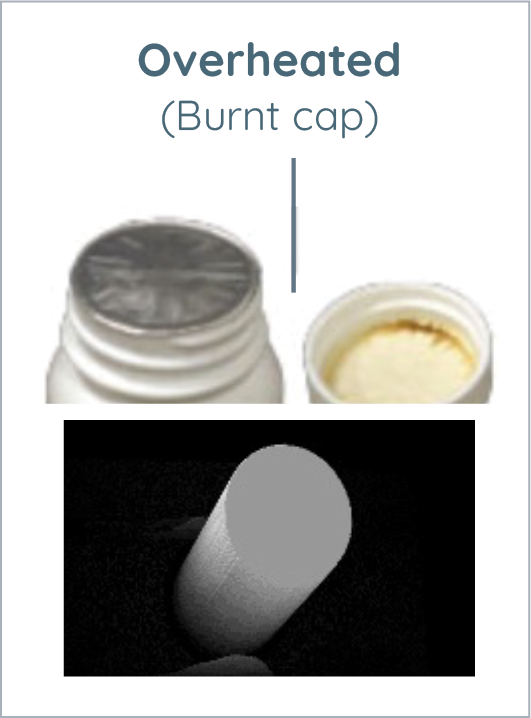
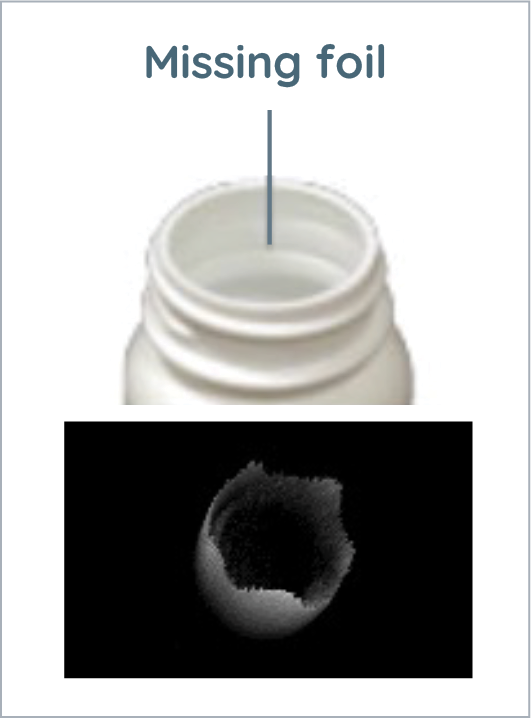
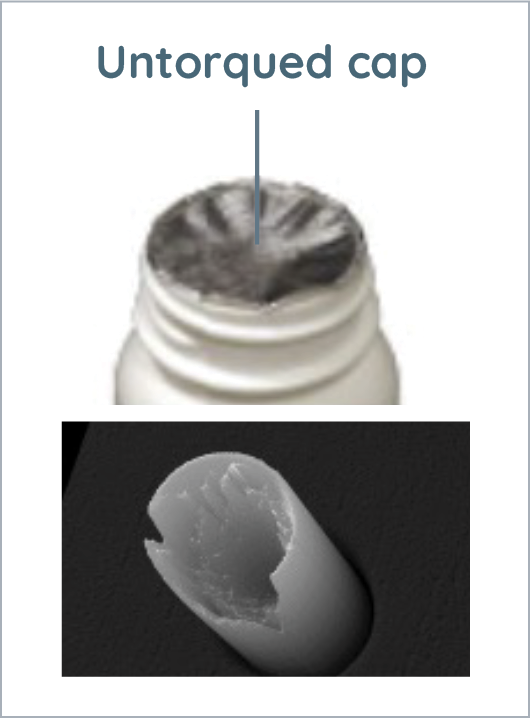
Reference scans of proper induction sealing integrity
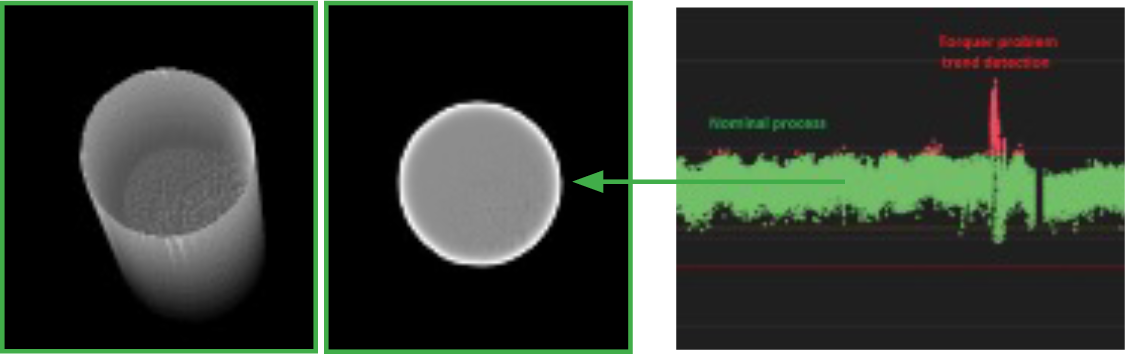
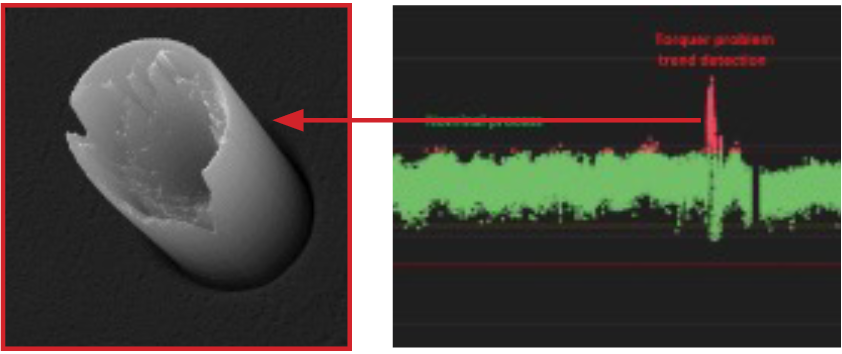