Proven Technology, Coming to a Production Line Near You
Thermal imaging technology was originally developed for the defense industry and employed in military and security applications to scan the infrared spectrum, essentially revealing the invisible.
Yoran Imaging is among the first to implement this promising technology to substantially improve heat-sealing inspection processes. By converting real-time thermal imaging inspection into actionable, user-friendly intelligence, the system provides a bevy of benefits for manufacturers.
Say Goodbye to Sampling
Imprecise inspection by sampling has long been the norm on high-speed packaging lines. Yoran Imaging’s novel Process Analytical Monitoring system replaces manual sampling with automatic 100% product inspection – a cost-effective, comprehensive and contact-free quality control upgrade.
At the same time, the system provides unprecedented levels of packaging line insight that can be used for ongoing production improvements and increased output. In doing so, the technology transcends manual limitations, matching the pace of live operations to ensure continuous quality and efficiency.
Seamless Integration that Protects Brand Reputation
Engineered for 100% inline installation, the plug-and-play Process Analytical Monitoring system is designed to integrate seamlessly into existing production lines. Quick to set up and easy to operate, it immediately begins to enhance quality control and operational efficiency.
The hardware agnostic, easily maneuverable system profoundly decreases the risk of defective reputation-damaging products reaching the public. The result is safeguarded brand integrity and enhanced customer trust.
Data Capture for Continuous Production Improvements
User-Friendly Data
Productivity also can be substantially increased, with user-friendly data alerting operators when preset quality or OEM parameters are degrading, providing guardrails and guideposts that minimize machine downtime through informed preemptive measures. This “uptime is money” benefit has led several major manufacturers to adopt the technology. To date, our systems have scanned over 1.7 billion products, analyzing production processes and rectifying defects in real time to guarantee that only good products make it to market.
Empowering Line Operators
Technological hurdles and cost-benefit limitations have delayed the adoption of data capture in certain facets of production. By translating volumes of filling and heat-sealing data into real-time, dashboard-ready metrics, Yoran Imaging’s system overcomes longstanding ROI hesitancies by empowering line operators to effectively preempt out-of-spec products or equipment failures before they occur.
Analytical Monitoring
Deploying the Process Analytical Monitoring system yields positive ROI within just 3.5 months, transforming production efficiency, enhancing cost management, and saving an estimated $1.7M in product costs every year.
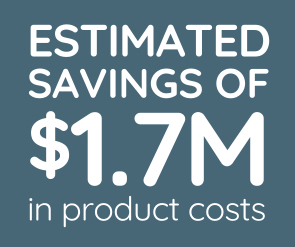
Waste Reduction & Sustainability Made Simple
Production Improvement Technology
Yoran Imaging’s patented production improvement technology prevents millions of defective products from being produced, saving customers tens of millions of dollars in potential financial loss via reduced product and packaging waste.
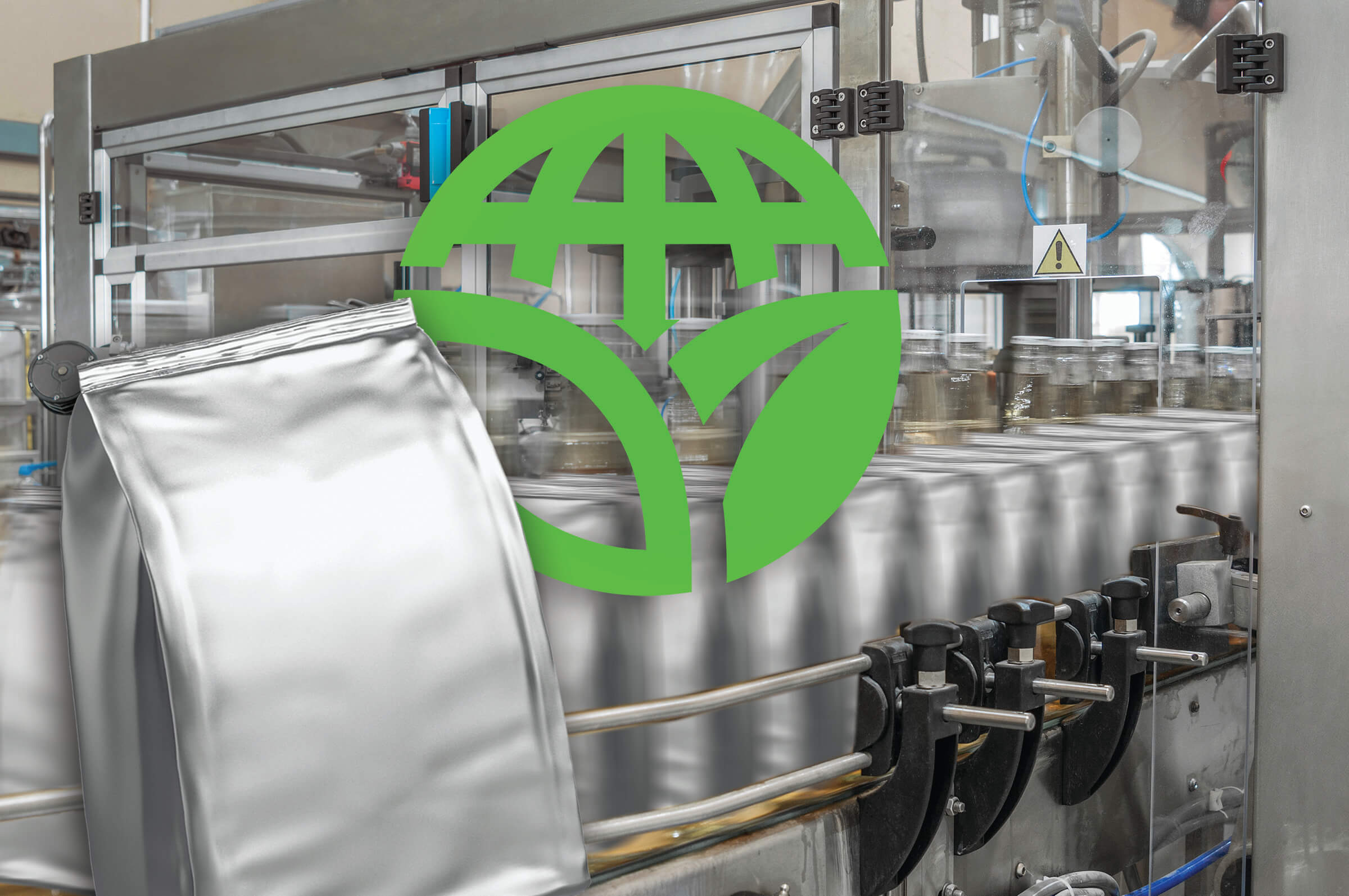
Crucially, the system also expedites the incorporation of more sustainable packaging materials by accelerating best practices development and process validation for recyclable heat-sealable substrates, including polyethylene (PE) and polypropylene (PP). It achieves this by addressing a noted challenge for transitioning to more sustainable substrates: narrower heat-sealing tolerances.
Discovering and maintaining the best-possible heat seal temperatures for various recyclable materials – which are often thinner and almost always more finicky than legacy substrates – has historically been a time-consuming, trial-and-error endeavor. By enlightening the overall process, the system gives production professionals the information needed to speedily incorporate more sustainable packaging materials.